Tape Production: Processes and Innovations in Manufacturing
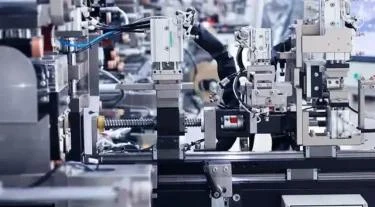
# Tape Production: Processes and Innovations in Manufacturing
## Introduction to Tape Manufacturing
Tape manufacturing is a complex process that involves multiple stages to produce adhesive products for various industries. From packaging to medical applications, tapes play a crucial role in modern life. The production of tape requires precision engineering, advanced materials science, and continuous innovation to meet evolving market demands.
## The Basic Tape Manufacturing Process
### 1. Material Preparation
The tape manufacturing process begins with the preparation of raw materials. The primary components include:
– Backing materials (paper, plastic films, or cloth)
– Adhesive compounds
– Release liners (for pressure-sensitive tapes)
– Additives for special properties
### 2. Coating Process
The coating stage is where the adhesive is applied to the backing material. There are several coating methods:
– Direct coating: Adhesive is applied directly to the backing
– Transfer coating: Adhesive is first applied to a release liner then transferred
– Hot melt coating: Adhesive is applied in molten form
### 3. Drying and Curing
After coating, the tape goes through drying ovens to remove solvents or water. For some adhesives, UV or electron beam curing may be used instead of thermal drying.
### 4. Slitting and Rewinding
The large rolls of coated material are then slit into narrower widths according to product specifications. Precision slitting ensures clean edges and consistent width.
### 5. Packaging
The final step involves packaging the tape rolls into various forms – from small consumer rolls to large industrial spools.
## Innovations in Tape Manufacturing
### Advanced Adhesive Technologies
Recent developments include:
– Environmentally friendly adhesives with reduced VOC emissions
– Bio-based adhesives from renewable resources
– Smart adhesives with temperature or pressure-responsive properties
### Automation and Industry 4.0
Modern tape manufacturing facilities incorporate:
– Automated quality control systems with machine vision
– Predictive maintenance using IoT sensors
– AI-driven process optimization
### Sustainable Manufacturing Practices
The industry is moving toward:
– Water-based adhesive systems
– Recyclable and biodegradable tape materials
– Energy-efficient production processes
## Quality Control in Tape Production
Quality assurance is critical throughout the manufacturing process. Key parameters monitored include:
– Adhesive thickness and uniformity
– Peel strength and tack properties
– Temperature and chemical resistance
– Dimensional accuracy
## Applications of Manufactured Tapes
Modern tape products serve diverse industries:
– Packaging (box sealing, bundling)
– Construction (masking, mounting)
– Electronics (conductive, insulating)
– Medical (surgical, wound care)
– Automotive (assembly, noise reduction)
## Future Trends in Tape Manufacturing
The tape manufacturing industry continues to evolve with:
– Nanotechnology-enhanced adhesives
– Self-healing adhesive systems
– Integration of smart sensors into tape products
– Development of tapes for extreme environments
As demand grows for specialized adhesive solutions, tape manufacturers will continue to innovate in materials, processes, and applications to meet the needs of an increasingly complex industrial landscape.
Keyword: tape manufacturing